Key instruments and sensors revolutionise aerospace operations
September 1, 2023 11:24 am
Prashant Sinha, Head of Marketing, WIKA India, talks about the precise engineering that meets data-driven insights in the aerospace realm. Aerospace instrumentation and control systems have emerged as the backbone of modern aviation that withstands extreme conditions, while data acquisition empowers predictive maintenance, ensuring safety and innovation in aviation.
What is the role of instrumentation and controls in the aerospace industry?
Instrumentation and controls are crucial in the aerospace sector, as they are responsible for collecting, overseeing, and processing data about diverse factors and circumstances during flight. These setups ensure aerospace crafts’ secure and effective functioning by delivering real-time information to pilots and engineers, thus empowering them to make well-informed choices and modifications. They play a significant role in flight control, navigation, guidance, and overall craft performance. These setups are integrated into various technologies, encompassing sensors, actuators, avionics, and communication networks, to closely monitor critical variables such as altitude, velocity, temperature, and fuel levels. These technological advancements also enhance awareness of the surroundings, increase safety, and curtail fuel consumption. In the aerospace domain, instrumentation and controls are indispensable for achieving reliable and accurate operations.
What are some of the key instruments and sensors used in aerospace applications?
Various instruments and sensors are employed in the aerospace sector to gauge and supervise critical parameters. These encompass temperature gauges, pressure detectors, and fuel flow gauges, among other examples. These tools facilitate accurate manoeuvring, management, and performance tracking of aerospace crafts. On a global scale, instruments and sensors have become pivotal in multiple aerospace applications, delivering essential information about altitude, velocity, orientation, and position.
Some of the WIKA products used in the aerospace industry are:
- Force transducers for electric actuators and drives to help make air travel more sustainable
- Pressure transducers for jet engines’ ICE detection monitors
- Aerospace load pins for a spacecraft’s flight control system
- Direct drive pressure gauges for aerospace and military oxygen systems
- A battery-free passive RFID wireless sensing device to easily check an aircraft’s tire pressure
- A wireless temperature sensor that can withstand temperatures from –40°F to 257°F (–40°C to 125°C).
How are control systems utilised in aerospace vehicles for flight control, navigation and guidance?
Control systems within aerospace vehicles are vital for upholding stability, guiding flight, and ensuring precise navigation and direction. Some of the key control systems that optimise the functioning of an aircraft encompass:
Airflow sensors: These instruments gauge airspeed and orientation, delivering essential insights into aerodynamic analysis, engine efficiency, and flight control systems. They play a crucial role in guaranteeing aircraft and spacecraft’s secure and efficient functioning.
Temperature monitors with switch contacts: In flight settings, these devices oversee temperature thresholds in critical components such as engines. Once the temperature surpasses predetermined limits, these switches activate warning signals, averting overheating. This mechanism ensures optimal performance and safety in aerospace systems.
Pressure sensors: These are integral to aircraft for assessing altitude, computing airspeed, and managing cabin pressure. Their presence enables precise altitude determination, a pivotal factor in navigation and approach. Moreover, they contribute to maintaining safe cabin pressurisation across different altitudes.
WIKA offers an extensive array of temperature gauges and pressure switches tailor-made for aerospace applications. These sensor-driven devices anticipate temperature variations and incorporate mechanisms that prompt preemptive actions and trigger alarms during pressure surges. Their efficacy is particularly pronounced in dynamic environments, ensuring continuous safety throughout the operational process.
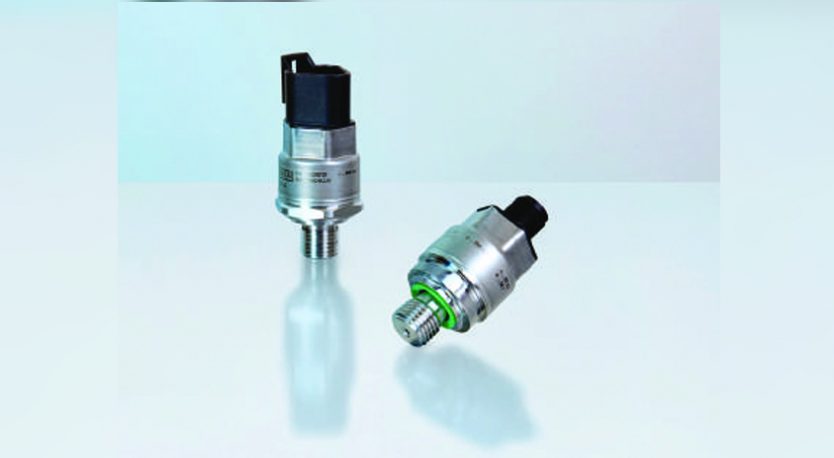
How do aerospace instrumentation and control systems handle extreme environmental conditions, such as high temperatures, vibrations and pressure?
Aerospace instrumentation and control systems are intricately designed and engineered to endure and perform efficiently within extreme environmental situations. They are crafted to withstand high temperatures, vibrations, pressures, and other demanding factors encountered during activities like space travel, flights at high altitudes, and re-entry into the atmosphere. Specialised materials, coatings, and isolation techniques are employed to shield delicate components from these conditions and uphold their operational integrity and dependability.
Materials resistant to high temperatures, heat shields, and cooling mechanisms are employed to prevent excessive heating. Methods to dampen vibrations and absorb shocks are implemented to counteract mechanical strains. Enclosures sealed against pressure are also utilised to shield components from elevated pressures, and sophisticated calibration algorithms are applied to uphold accuracy within these challenging settings.
These combined strategies empower aerospace systems to function flawlessly amidst elevated temperatures, vibrations, and pressures, ultimately ensuring the safety of both the flight and the crew under these demanding circumstances.
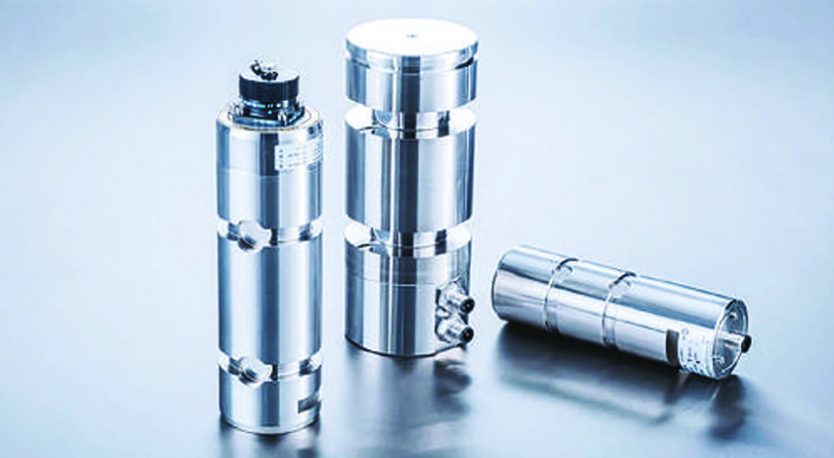
What are the typical data acquisition and analysis techniques used in aerospace instrumentation?
Data acquisition in aerospace instrumentation involves collecting information from diverse sensors and instruments installed on the aircraft. Subsequently, this data undergoes processing, examination, and interpretation to yield insights into the vehicle’s overall health, safety, and performance.
Advanced sensors collect various data points, including temperature, pressure, acceleration, and more, to comprehend flight conditions and enable real-time monitoring and analysis. Cutting-edge methodologies for data analysis, encompassing signal processing, statistical evaluation, and machine learning, are utilised to derive meaningful trends and identify potential concerns that warrant further exploration and enhancement. This process plays a pivotal role in the predictive maintenance of the aircraft, ultimately amplifying its safety.
The combined data acquisition and analysis activities constitute the foundation of aerospace instrumentation, allowing engineers to refine systems, ensure safety, and stimulate innovation within the aviation industry.
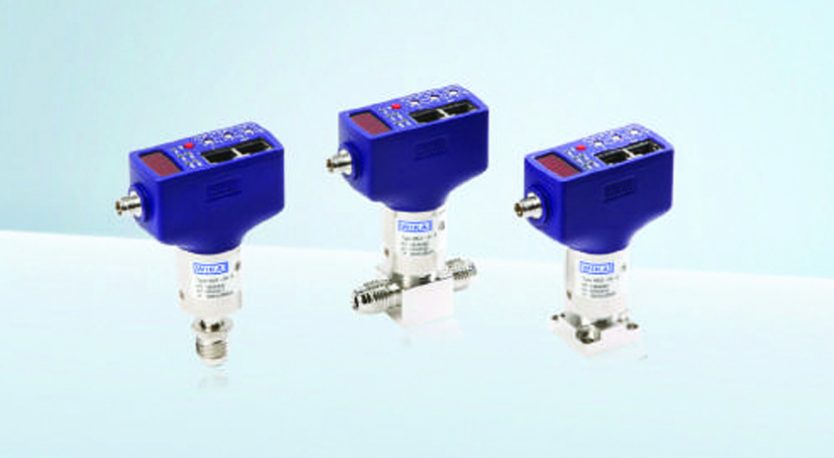
How do fault detection and redundancy play a role in aerospace instrumentation and control systems to ensure reliability and safety?
In aerospace instrumentation and control systems, ensuring the dependability and safety of the vehicle within challenging settings necessitates a strong focus on identifying faults and incorporating redundancy. Incorporating backup functionalities through redundant sensors and control systems is a crucial measure to counteract failures. This involves duplicating vital components like sensors and processors, guaranteeing uninterrupted functionality even when one element experiences a malfunction. Algorithms for fault detection are deployed to oversee the system’s operation, activating appropriate responses upon identifying anomalies or glitches. This approach minimises the likelihood of accidents and bolsters the system’s overall resilience. These technologies are pivotal in maintaining the optimal performance of an aircraft, averting potential calamities, and ensuring the well-being of both the crew and the vehicles.
What are the latest trends for correction and predictive maintenance in aerospace applications?
The aerospace industry has made great strides with technological advancements in correction and predictive maintenance. Some of the key areas that are making major progress are:
- Enhancing aircraft safety using machine learning algorithms to enable precise anomaly detection and fault prediction
- Preventing potential issues, minimising downtime and enhancing safety with proactive maintenance strategies
- Leveraging data analytics to forecast component failures, optimising maintenance schedules and resource allocation with robust predictive maintenance
- Receiving continuous insights into equipment health and facilitating timely interventions with real-time monitoring and diagnostics through advanced analytics.
These technologies are reshaping how maintenance is conducted in aerospace, ensuring streamlined operations, cost savings, and increased reliability by leveraging the potential of data-driven insights.
Cookie Consent
We use cookies to personalize your experience. By continuing to visit this website you agree to our Terms & Conditions, Privacy Policy and Cookie Policy.