Sulzer 55 MW generator winding upgrade improves reliability and reduces unscheduled stoppages
October 12, 2023 12:28 pm
Large-scale manufacturing facilities in remote areas often rely on independent power generation sources to deliver the vast amounts of energy needed for operations. Turbo generators are often the cornerstones of these power sources. However, if they suffer unforeseen downtime, this reliance can result in a 100% loss of production. This was the situation faced by an Indonesian cement producer, which turned to Sulzer to resolve the failure quickly and upgrade its generator to protect uptime.
Ground to an unscheduled stoppage
The breakdown of the 55 MW generator was caused by strand-to-strand faults that eventuated into a stator connection phase ground fault. Due to the excessive amount of winding oil contamination from a leaking bearing labyrinth seal, the ground fault flash resulted in a stator fire. As this was the only power source for the facility, production was immediately halted, risking the delivery of orders to customers. Any order obligations would need to be met by other facilities, placing stress on the cement producer’s regional operations. To resolve this, root cause analysis and a rapid temporary repair was requested by the cement plant management, followed by a full stator rewind at a more convenient time to suit their production commitments
A thorough investigative inspection by Sulzer’s experts revealed that the failure was attributed to the stator winding design having parallel stranding, which caused high circulating currents. The tracking across the surface of the stranding resulted in excessive winding temperature, eventually instigating the ground connection phase fault.
Rapidly responding to an urgent repair
Due to a proven track record supporting the customer’s various production facilities, Sulzer was awarded the repair and upgrade project by direct appointment for the scope of winding and incorporating a 360° Roebel bar. A leading independent service provider for rotating equipment, Sulzer is a global expert in generator repairs and upgrades for steam and gas turbines with a local presence in Indonesia.
The technical proposal of utilizing 360° Roebel bars presented by Sulzer’s global technical team convinced the cement plant management that it was the most optimal solution, along with timeline assurance. Furthermore, the customer was aware of Sulzer’s robust global supply chain, which would expedite the project and support the generator long into the future. Compounding these advantages, Sulzer could offer a lead time of 10 weeks, while other vendors were still offering parallel strand conductors and completion schedules of several months.
To get the plant temporarily operational as soon as possible, Sulzer quickly completed a partial repair to the failed stator windings. This allowed the cement producer to work through their material stockpile and meet existing orders – which helped to reduce any loss of revenue caused by the generator failure. Illustrating its global engineering flexibility, Sulzer was the only vendor which could offer this partial repair – a testament to the company’s customer centricity.
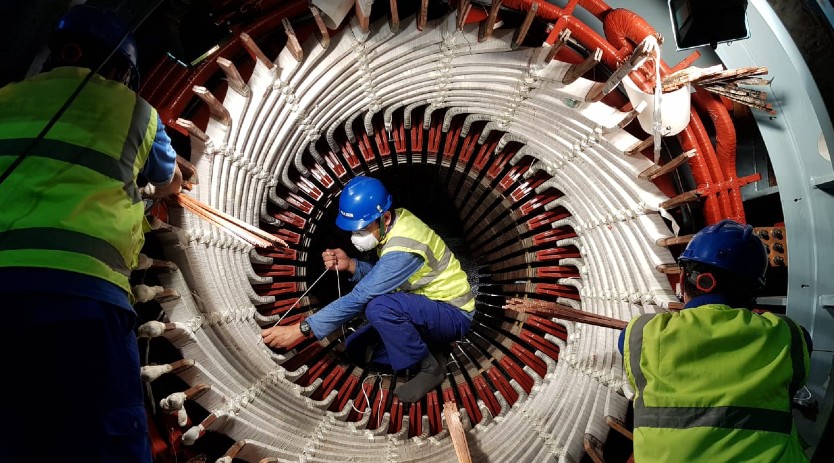
A question of half-bar engineering and manufacturing
Meanwhile, Sulzer worked on re-designing the new stator windings. The 360° Roebel bars would eliminate future circulating current problems compared to the original designed parallel conductors. However, this required overcoming numerous engineering challenges due to the short length of the stator core
First of all, fitting the Roebel bars into the short stator core was going to take exceptional technical expertise. The OEM did not offer Roebel bars for this generator model, so Sulzer would be breaking new ground. Precision reverse engineering was required to ensure that the new top and bottom bars with a 360° Roebel would fit. Finally, the replacement bars would have to be engineered and manufactured specially for this generator. Thankfully, all these requirements were accomplished in-house by Sulzer’s experienced engineering and design team.
A generator upgrade uncoiled
Leveraging its global network, Sulzer Indonesia connected with the Birmingham Service Center in the UK, one of the numerous facilities within Sulzer which has the engineering and manufacturing facilities for high voltage stator coils and half bar production, backed by a comprehensive database and automated design capabilities. This overseas collaboration is common practice at Sulzer, with each facility in its network offering seamless access to the full global capabilities of the company.
Using data collected from the stator and existing top and bottom bars, the Birmingham Service Center reverse engineered the winding to incorporate a 360° Roebel. With this complete, engineers precision manufactured a half stator section to confirm the correct fit of winding pitch to expedite installation on-site. Sulzer produced 48 top bars and 48 bottom bars in 10 weeks – a lead time much shorter than the several months quoted by other service providers.
To ensure a continuous workflow and minimize the duration of the winding process, the bottom bars were shipped first, followed by the top bars. This phased delivery allowed the Sulzer Indonesia team to complete the generator rewind sooner, as waiting for a single shipment would’ve increased the project timeline by several days. Furthermore, this scheduling ensured that the project could be completed within a planned shutdown period of 10-12 weeks, reducing disturbance to their production operations.
A concrete foundation for reliability
The benefits of switching to Roebel bars were quickly apparent. Winding temperatures were greatly reduced, allowing the generator to be run more efficiently, providing energy cost savings to the cement plant. In terms of reliability, electrical circulating currents were all but eliminated, greatly reducing the risk of any future premature failures. Reduced winding temperatures also meant less thermal stresses on the winding insultation, improving service life. With the generator up and running, the pressure on the customer’s other facilities was alleviated too, with the plant now operating at full capacity.
When critical equipment suffers a breakdown, operations and production are always at risk. However, by trusting in the global expertise of Sulzer, this cement producer was able to avoid the worst-case scenario. The customer centric approach of Sulzer prioritized the needs of the cement producer, minimizing any impact to operations or business reputation. Beyond providing a stop-gap repair to keep production running, Sulzer employed its coil manufacturing and reverse engineering skills to build a new foundation for future generator reliability.
Cookie Consent
We use cookies to personalize your experience. By continuing to visit this website you agree to our Terms & Conditions, Privacy Policy and Cookie Policy.