Engineered to deliver, enhanced by VERICUT
July 3, 2023 5:41 pm
The article highlights SPC also uses VERICUT to manage production capacity at the facility. The log and run-time estimation output by VERICUT allows SPC to review better and optimise the balancing of workloads and manufacturing capabilities.
The VERICUT software developed by CGTech has provided Hyde Aero Products Ltd. with a reliable and reassuring safety net, instilling confidence in their operations for over 20 years as one of the UK’s largest independent engineering companies, Hyde Aero Products Ltd. has developed a strong reputation for designing, manufacturing and assembling components for a wide range of customers, services and systems. It varies from manufacturing prototype and test components for the medical and tooling industries to the fast response AOG deliveries for aviation and defence clients. Hyde Aero Products Ltd has an established customer base, supported by its highly developed engineering skill set and the verification capabilities of VERICUT.
Hyde Aero Products Ltd., a conglomerate of more than 20 manufacturing units specialising in various aspects of metallic component manufacturing and processing, relies on VERICUT CNC simulation, verification, and optimisation software at multiple locations within the company.
In particular, Stoneswood Precision Components Ltd (SPC), which specialises in the subtractive manufacturing of soft and hard metal aerospace components, has harnessed the functions within VERICUT to deliver high-quality components for the first time.
Simplicity and Reliability
To achieve the ‘right-first-time’ manufacturing ethos at Hyde Aero Products Ltd, VERICUT is essential and has cemented its place as the final check before any code leaves the engineering department. Its accurate, high-resolution collision detection, detailed measuring and analysis ensure safe and efficient NC programs are created and issued to the shop floor.
Machine operators and programmers have confidence and peace of mind knowing that VERICUT has independently reviewed NC programs. ‘First off’ components and ‘prove outs’ pass through various departments within the facility with ease, as dimensional accuracy and overall quality is verified and assured.
Rob Westley, Senior Technical Engineer at SPC, explains, “From small 3-axis aluminium brackets to large, high-value 5-axis titanium structural components, everything runs through VERICUT. No single program, no matter how short, is output to the shopfloor without first being checked and having the final VERICUT seal of approval.”
Delivering better products and enhanced components through continuous improvement is a top priority for Hyde Aero Products Ltd. Likewise, the engineering teams at sites such as SPC have also seen VERICUT continually improved into an easy-to-use platform that independently and accurately verifies all machining types – from simple face milling to complex 5-axis closed wall barrel cutting toolpaths. It is also a great tool for training employees and sharing knowledge. The live simulation cut the stock to display in the software provides a way to visualise and demonstrate machining strategies and toolpaths to shopfloor machine operators. In addition, CGTech’s VUE (Vericut User Exchange) meeting and reliable technical support team have been invaluable to the installation of VERICUT over the years with the engineering team at SPC.
“The simplicity of VERICUT and the speed at which it can be used has led to it never being seen as a burden to the programming element of the production chain,” explains Tom Whitbread, SPC Technical Engineer. “Over my five years as a programmer and through my SPC apprenticeship program, VERICUT has always captured my training errors and helped me develop my skills for program optimisation and enhancing the quality of the components I engineer”.
Shortening Tools and Expanding Utilities
Using the Tool Management database, SPC creates accurate, detailed assemblies of tools perfectly scaled to the cutters. Engineers can then optimise tooling to produce a higher quality product in a shorter time frame (through the use of shorter cutters). Likewise, the high resolution and detailed analysis of the proximity between tool holders, stock and fixturing has also led SPC to manufacture complex components through standardised work holding methods. Fixtures can be used on multiple components through the confidence brought about by VERICUT, ultimately reducing manufacturing costs.
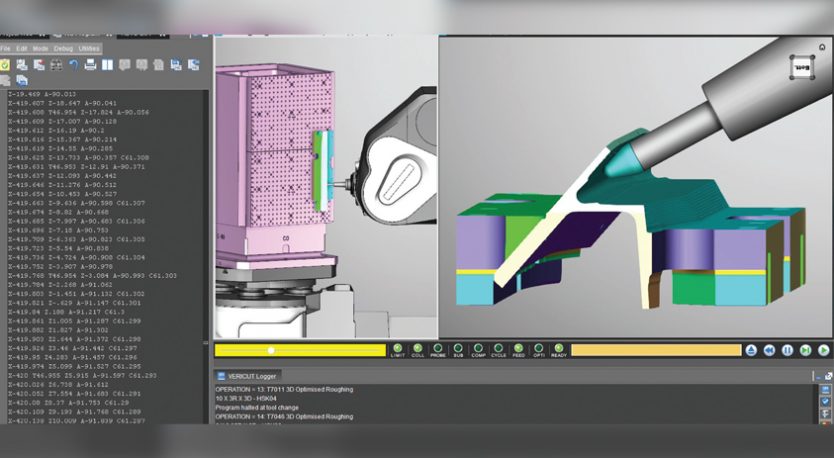
Assurance of AUTO-DIFF
One of the most powerful modules in VERICUT is AUTO-DIFF, which SPC uses on every job. The ability to spot even minor human errors during programming, or an issue with a particular toolpath or post-processing script, can prove vital. Levels of scrap within SPC have been greatly reduced by AUTO-DIFF, which highlights gouges or excess material after simulating the machining of a component. Quickly analysing the full component and verifying that it conforms to customer-supplied data without cross-referencing a drawing or measuring individual features has improved the quality and accuracy of programs produced. John Kelly, Senior Manufacturing Engineer, says, “The level of confidence brought about by VERICUT’S AUTO-DIFF feature has increased the complexity of the programs that we can produce, allowing us to ‘push the envelope’ to try new strategies and techniques on actual components rather than limiting research and development to off-the-job testing pieces and theoretical scenarios.”
The improved level of confidence brought about by VERICUT with features such as AUTO-DIFF also helps SPC optimise and re-engineer legacy components using the latest technology and strategies available, achieving more efficient and effective methods of manufacture and further improving the high level of component quality.
Capacity and Production Management
SPC also use VERICUT to manage production capacity at the facility. The log and run-time estimation output by VERICUT allows SPC to review better and optimise the balancing of workloads and manufacturing capabilities of the various machining cells within the factory. The engineering department logs the output estimated run time from VERICUT and is used to optimise the ‘lights-out’ production and overnight manufacture of components in the business. This way, long-running components can be manufactured during ‘lights-out’ production hours, whereas shorter jobs can run during the daytime.
This understanding of specific component production hours, alongside implementing two new Hermle C400 5 axis CNC machines, each with 15 pallets, creates an incredibly efficient method of manufacturing high quality, tight tolerance, small-to-medium-sized aerospace components. Component probing, also simulated in VERICUT, gives an SPC a further boost in confidence, especially through the ‘lights-out’ periods of manufacture. Chris Lannigan, Business Development Director, says, “This ability to better understand and analyse both the quoting and manufacturing process chain has further strengthened the business’s short lead time machining capabilities”.
To remain competitive and cost-effective in this ever-changing manufacturing industry, the quoting and costing of new work and projects by SPC have always been critical to the business. This is strengthened by VERICUT’s estimated run time output alongside useful shopfloor feedback helping to fine-tune the company’s quoting capabilities for new projects and customers – allowing for more accurate project pricing and estimated delivery dates.
Overall, VERICUT CNC simulation, verification and optimisation software allows Hyde Aero Products Ltd to maintain its reputation as a ‘one-stop shop for all manufacturing needs’ for various customers and industries. Individual machining sites such as SPC uphold high standards and customer expectations through the different engineering review and analysis features and capabilities provided by VERICUT. VERICUT gives confidence and vital feedback in helping the progression of SPC in the competitive aerospace industry.
For more information, visit CGTech at www.cgtech.co.uk
Expertise shared by: Tom Whitbread, Technical Engineer (SPC), Stoneswood Precision Components Ltd.
Cookie Consent
We use cookies to personalize your experience. By continuing to visit this website you agree to our Terms & Conditions, Privacy Policy and Cookie Policy.