The IIoT revolution in manufacturing
September 30, 2023 3:02 pm
In the words of Anil Kumar, Director at Inovance Technology, the IIoT is revolutionising manufacturing. It connects machines, boosts efficiency, enhances safety and security, optimises supply chains, enables predictive maintenance, and drives significant cost reductions.
In what ways is the manufacturing sector being transformed by the influence of IIoT?
The Industrial Internet of Things (IIoT) has emerged as a potent force in the digital realm, particularly within the manufacturing and automation sectors. It is revolutionising global manufacturing by linking machinery and equipment to the internet, resulting in smarter and more efficient operations. At Inovance, IIoT is designed to connect factories and their processes in real-time via the internet, fostering transparent data sharing and enhancing operational performance. IIoT is a pivotal technology in the industrial revolution, propelling progress and innovation in various industries.
For instance, factories can utilise sensors to anticipate machine maintenance needs, thus preventing unexpected breakdowns. IIoT also aids in optimising processes, such as fine-tuning assembly line robots to reduce errors. It improves inventory management, boosts energy efficiency, provides visibility in the supply chain, enhances product quality through continuous monitoring, elevates employee safety, enables mass customisation, and facilitates remote monitoring and control of equipment. In essence, IIoT simplifies manufacturing processes, elevating productivity and nurturing innovation across diverse sectors.
Recognising the profound influence and wide-ranging advantages of IIoT technology, Inovance has recently unveiled the IoT-WL135 device. This state-of-the-art equipment is a central player in industrial manufacturing, enabling real-time data collection and monitoring, predictive maintenance strategies, and comprehensive process optimisation. Its standout feature lies in its seamless integration capabilities, allowing it to interface with existing systems smoothly. This feature proves invaluable to manufacturers seeking to modernise their operations without disruptions.
What challenges are manufacturers facing while implementing IIoT technologies in their production processes?
Manufacturers need help with incorporating IIoT technologies into their production processes. To begin with, there is the potential for high expenses associated with establishing IIoT systems. Secondly, it is essential to prioritise data security due to the involvement of confidential and sensitive information. Overcoming challenges related to integrating these systems with existing ones and ensuring scalability as the business expands is also crucial. Effective data management and analytics, bridging the skills gap, and complying with industry regulations all assume significant importance. Manufacturers must also guarantee the reliability of IIoT systems to minimise downtime, address privacy concerns, and navigate the organisational shift as employees adapt to new technologies.
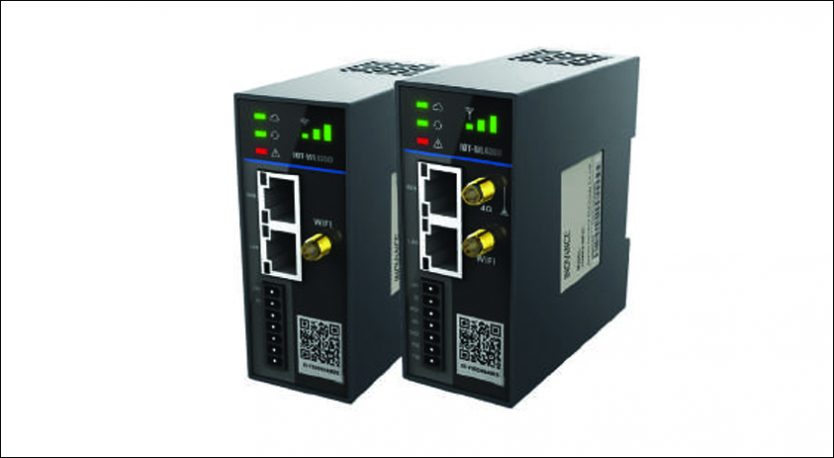
How does IIoT enhance predictive maintenance within the manufacturing realm, resulting in minimised downtime and significant cost savings?
Predictive maintenance, which involves anticipating equipment failures, has gained fresh impetus with the advent of the Industrial Internet of Things. IIoT enhances predictive maintenance by harnessing real-time data from sensors and connected devices. This technology not only assesses the condition of machinery but also delivers a continuous stream of data for more precise predictions. In contrast to conventional methods, which may have encountered limitations due to the sheer volume of data, IIoT’s capacity to handle and process extensive data sets allows for more advanced and accurate predictive maintenance strategies. The convergence of predictive maintenance and IIoT results in more efficient equipment monitoring, reduced downtime, and substantial cost savings for manufacturing industries compared to traditional maintenance approaches. Here are five key ways in which IIoT enhances predictive maintenance:
· Real-time Equipment Monitoring: IIoT sensors continuously monitor the condition of machines, providing real-time data.
· Data analytics: Advanced analytics and machine learning algorithms process the collected data, identifying patterns indicating potential equipment failures or maintenance needs.
· Predictive alerts and notifications: When the analytics detect any issues, IIoT systems send alerts and notifications to maintenance teams, allowing them to address problems before they lead to major breakdowns.
· Proactive maintenance scheduling: Instead of relying on fixed maintenance schedules, IIoT enables maintenance to be scheduled based on the actual condition of equipment. This minimises unnecessary servicing and reduces downtime.
· Resource optimisation: With predictive maintenance, resources such as labour, spare parts, and maintenance equipment are allocated more efficiently. This optimisation reduces operational costs and extends machines’ lifespan, resulting in significant cost savings over time.
What impact does the integration of IIoT devices with AI have on manufacturing operations?
Integrating IIoT (Industrial Internet of Things) and AI (Artificial Intelligence) integration in the manufacturing sector brings numerous benefits. It has a profound impact, spanning from predictive maintenance to data analytics. AI optimises production processes by utilising IIoT data, resulting in heightened operational efficiency. Manufacturers can reduce waste, improve product quality, and streamline product customisation, catering to specific customer needs more effectively. Furthermore, AI-driven quality control ensures the real-time identification of defects, ensuring consistent product quality.
Safety in manufacturing also sees significant enhancements as AI processes IIoT sensor data to detect and respond to safety hazards swiftly, creating a safer workplace. Data analytics is another pivotal outcome, as AI’s ability to analyse extensive volumes of IIoT data reveals valuable insights and patterns that inform data-driven decision-making. Continuous improvement is fundamental to this integration, as AI consistently learns from IIoT data, facilitating ongoing process optimisation, cost reduction, and innovation. Ultimately, these advantages provide a competitive edge, enabling manufacturers to operate efficiently, adapt to market fluctuations, and make real-time decisions in an ever-evolving industrial landscape.
To address concerns related to safety and security, Inovance’s IoT-WL135 device proactively identifies potential safety risks and mitigates them, contributing to a safer work environment. Additionally, its ability to reduce costs by minimising downtime significantly benefits manufacturers. By preemptively detecting issues and enabling swift responses, it not only saves valuable time but also financial resources.
One of the most compelling features of the IoT-WL135 is its capability to offer remote monitoring and instant alerts. This means manufacturers can closely monitor their operations, even from a distance, and receive immediate notifications when issues arise.
How does cloud computing contribute to enabling the broad acceptance of IIoT solutions in manufacturing?
Cloud computing is crucial in promoting the adoption of Industrial Internet of Things (IIoT) solutions in the manufacturing industry. IIoT generates vast data streams from various sensors, devices, and machinery. Cloud platforms offer adaptable and cost-effective storage solutions, allowing manufacturers to manage and supervise data without substantial investments in physical infrastructure. This scalability will enable companies to quickly adapt to changing data requirements while using powerful data processing and analytics capabilities.
With the increasing demand for smart factories, how will integrating IIoT in manufacturing reshape the industry’s landscape?
Implementing IIoT technology offers significant advantages for companies in the manufacturing sector, simplifying various processes such as real-time monitoring, tracking, management, predictive maintenance, process optimisation, and seamless integration across their operations. Furthermore, IIoT systems can enhance safety and security, optimise supply chains, improve quality control, enable predictive maintenance, and lead to substantial cost savings.
Inovance’s IoT-WL135 device is designed to boost machine efficiency, increase reliability, and elevate customer satisfaction. Its proactive problem-solving approach ensures identifying and resolving potential issues before they escalate, benefiting all manufacturers seeking to optimise their processes and deliver top-notch products and services to their customers.
Cookie Consent
We use cookies to personalize your experience. By continuing to visit this website you agree to our Terms & Conditions, Privacy Policy and Cookie Policy.